Home » V Band Clamp Roll Forming Machine » Locking Inner Ring Clamp Roll Forming Machines
Locking Inner Ring Clamp Roll Forming Machines
- Speed: 30 Components For One Minute
- Hoop Barrel Clamp Ring Material: 304 Stainless Steel
- Thickness Of Coil: 0.8mm To 3mm
- Material Of Rollers: Cr12Mov
- Width Of Coil: 30mm ~ 120mm
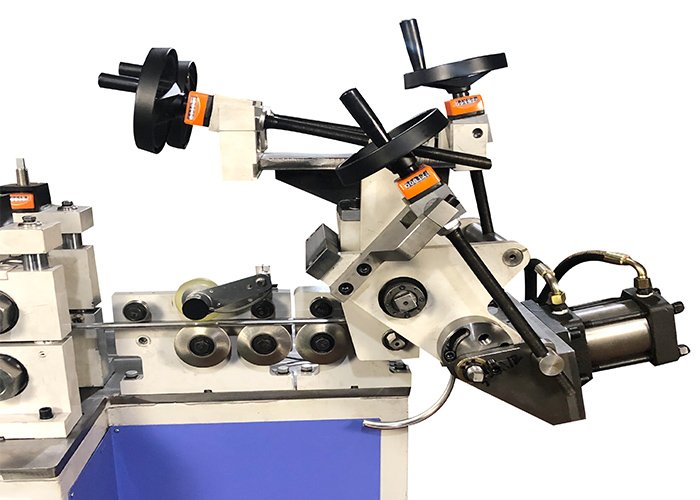
Introduction of Locking Inner Ring Clamp Roll Forming Machines
- Introduction of the ring clamp: It consists of a shallow integral v-flange retainer and two bands for positioning and securing the selected closure type. The ring clamp is light in weight and compact in structure, which is widely used in various industrial sectors to pull and fix two circular flanges. Compared with the v-clamp, the ring clamp is a low-cost clamping solution.
- Introduction of our machines: Two V-shaped flanges are produced by one-step roll forming and cut to at the end of the machine. We adopt frequency converter motor or servo motor to control speed, PLC and HMI to control flanges length and quantity.
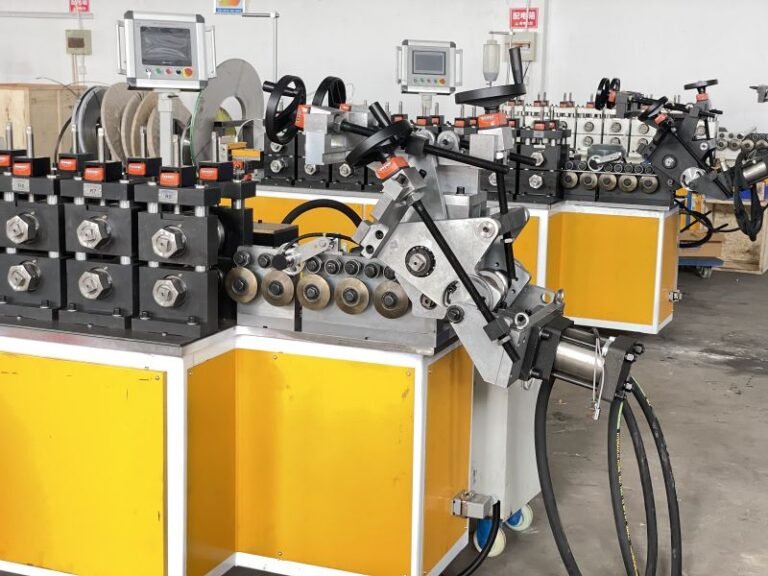
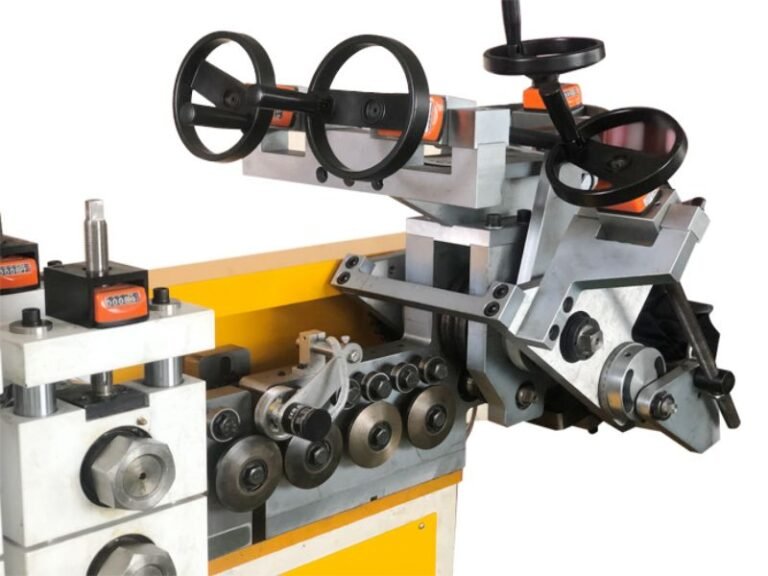
Product Application
This kind of roll forming machine uses stainless steel as raw material, through decoiler, straightening, roll forming and cutter processes, it can produce all kinds of clamping rings.
Machine Parameters
No | Items | Technical Requirements |
1 | Production Process
| De-coiler — Leveling — Roll Forming — Rolling Head — Cut off |
2 | Floor Area | 15×2.5×2(L×W×H)M |
3 | Feeding Direction | From Left to Right |
4 | Voltage | 380V,50Hz,3 Phase |
5 | Air Supply | Flow Rate:0.5m³/min; Pressure: 0-0.7MPa |
6 | Hydraulic Fluid | 46# |
7 | Gear Oil | 150# |
8 | Material of Strip | Stainless Steel |
9 | Width of Strip | ≤80mm |
10 | Thickness of Strip
| ≤2.8mm |
11 | Speed | 10 components per minute for diameter 378mm 15 components per minute for diameter 248mm 20 to 25 components per minute for diameter 115.8 to 127.4mm 20 to 25 components per minute for diameter 127.4 to 155.8mm 20 to 35 components per minute for diameter 72.6 to 148.8mm |
Technical Configuration
No | Items | Technical Requirements |
1 | Production Process
| De-coiler — Leveling — Roll Forming — Rolling Head — Cut off |
2 | Floor Area | 15×2.5×2(L×W×H)M |
3 | Feeding Direction | From Left to Right |
4 | Voltage | 380V,50Hz,3 Phase |
5 | Air Supply | Flow Rate:0.5m³/min; Pressure: 0-0.7MPa |
6 | Hydraulic Fluid | 46# |
7 | Gear Oil | 150# |
8 | Material of Strip | Stainless Steel |
9 | Width of Strip | ≤80mm |
10 | Thickness of Strip
| ≤2.8mm |
11 | Speed | 10 components per minute for diameter 378mm 15 components per minute for diameter 248mm 20 to 25 components per minute for diameter 115.8 to 127.4mm 20 to 25 components per minute for diameter 127.4 to 155.8mm 20 to 35 components per minute for diameter 72.6 to 148.8mm |
12 | Length Tolerance | ±0.25mm |
13 | Total Power | Around 25 KW |
Main Devices of Roll Forming Machines
No | Items | Model | Qty | Remark |
1 | De-coiler and Straightening Combine Device | LS-300F | 1 set |
|
2 | Roll Forming Device |
| 1 set |
|
3 | Guarding Cover |
| 1 set |
|
4 | Control System |
| 1 set |
|
Electric Elements Brand
No | Items | Brand | Remark |
1 | PLC | OMRON |
|
2 | HMI | WEINVIEW |
|
3 | Electric Elements | Schneider |
|
4 | Bearing | NSK |
|
5 | Main Motor | YASKAWA Servo Motor |
|
6 | Digital Position Display | SIKO |
|
Technical Configuration
No | Items | Technical Parameters | |
1 |
De-coiler
| Width of Strip | 30-100mm; |
Thickness of Strip | ≤2mm; | ||
Inner Diameter of Coil | ф480-520 mm(according to customer’s requirements); | ||
Outer Diameter of Coil | φ1300mm;Loading Weight:≤1T | ||
Expand Way | Manual | ||
Power | 3 KW | ||
2 | Straightening Device | Width of Strip | 30-100mm; |
Thickness of Strip | ≤2mm; | ||
Motor Power | 1.5 KW | ||
Speed | Max16m/min | ||
Roller Arrangement | 7 rollers | ||
Arrange mode | 4-Point Independent | ||
3 | Roll Forming | Forming Stations | 8 Stations |
Type of Driven | Gear | ||
Forming Rack: | The roller is adjusted by digital display. | ||
Station Pitch | 200mm | ||
Max. Feeding Width of Coil | 100mm | ||
Max. Thickness of Material | 2mm | ||
Diameter of Shafts | Φ50mm ,42CrMo (quenching and tempering) | ||
Material of Roller | Cr12,Hardness: HRC58-60° | ||
Main Driven Motor | 15KW | ||
Bending and Cutting Devices | 1 set | ||
Turkey Head Device | 1set | ||
4 | Guarding | Usage and characteristics | Safety protection device mainly aims at two parts of the protection, one part of the main forming machine protection, the use of aluminum profiles and transparent plexiglass, electrical control, etc. for the main forming machine safety protection; the other part of the automatic material rack and leveling position protection, the use of aluminum profiles and wire mesh for the overall protection of the equipment with only one outlet. |
Unique product configuration
1、Guide Roller Device
Accurate introduction of the first forming wheel, with digital display, detection of head and tail of coils.
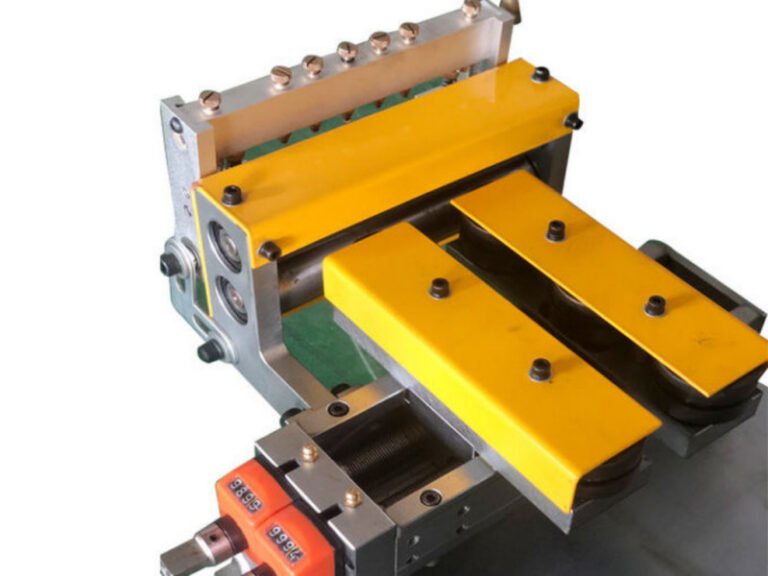
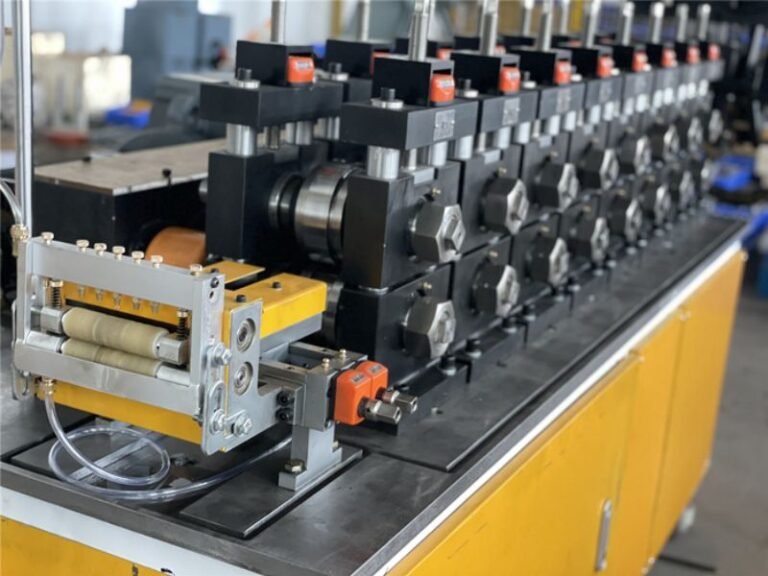
2、Lubrication system
The lubrication system for segment forming will be self-contained within the machine. The excess lubrication from the forming process will be re-circulated, filtered and re-used.
3、Special Gear Boxes Device
We optimized it and added a gearbox. The gears are in the gearbox to ensure sufficient lubrication, higher transmission accuracy and lower noise. The length accuracy we can achieve now can be guaranteed within 0.5mm.

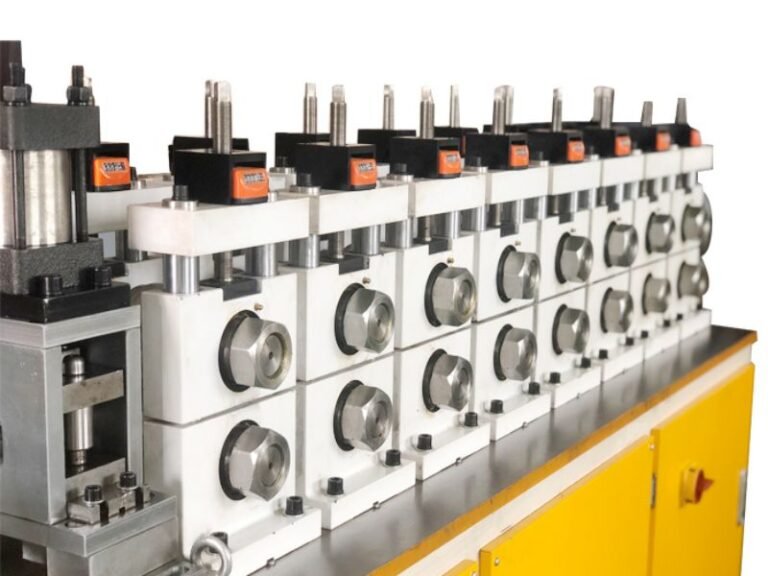
4、Guardings and Control System
All PLC programmes and any on-screen instructions must be in the English language.The operator controls will be mounted in a location, which best suits, the safe operation of the machine.
At least one Emergency stop will be fitted at the operator position and others, as the design requires.
The equipment will be run through a PLC with instructions/messages displayed on a small HMI screen. The control system should include, at minimum, the following:
The equipment will be run through a PLC with instructions/messages displayed on a small HMI screen. The control system should include, at minimum, the following:
- Machine operation monitoring.
- List of Inputs and Outputs and their condition
- Simple operator interface using push buttons or touch screen.
Where machine positions/settings are required for different products, these settings must be controlled via the HMI. The HMI will be used to call the correct program for the particular product with all machine settings automatically transferred. The program should also show digital readout’s of diameter, & pinch rollers position, etc.
Finished Products
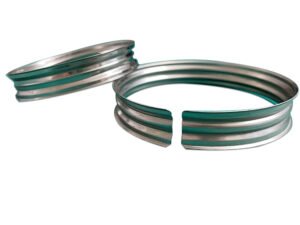
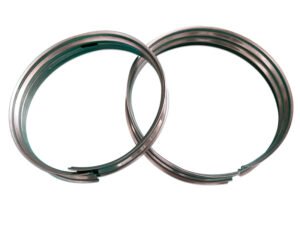
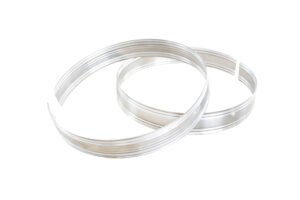
GET ONE-ON-ONE SERVICE
Free of charge to provide you with technical advisory services. Provide product samples, business profiles, credit certificates and other information. I invite customers to visit the company’s product design, product manufacturing process, product prototype, product testing facilities and quality management system