Home » Storage Rack Roll Forming Machine Collection » Shelf Back Layer Roll Forming Machine
shelf back layer Roll Forming Machine
- Type: Tile Forming Machine
- Production Capacity: 8-12m/min
- Use: shelf board
- Dimension(L*W*H): 7500*1200*1000mm
- Rolling thinckness: 0.7-1.2mm
- Core Components: Pressure vessel, Motor, Bearing, Gear, Pump, Gearbox, Engine
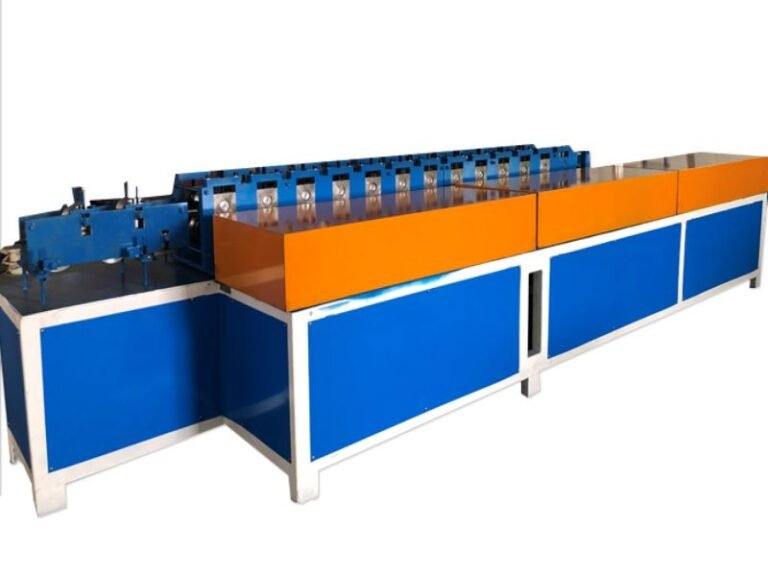
Description of shelf back layer Roll Forming Machine
The production line integrates uncoiling, leveling, forming, cutting, punching, receiving and related processes. The whole production line is controlled by PCL program.
The operator can select a preset program through the touch screen to automatically run the whole line. The operation methods include automatic control, manual control, separate operation and emergency stop.
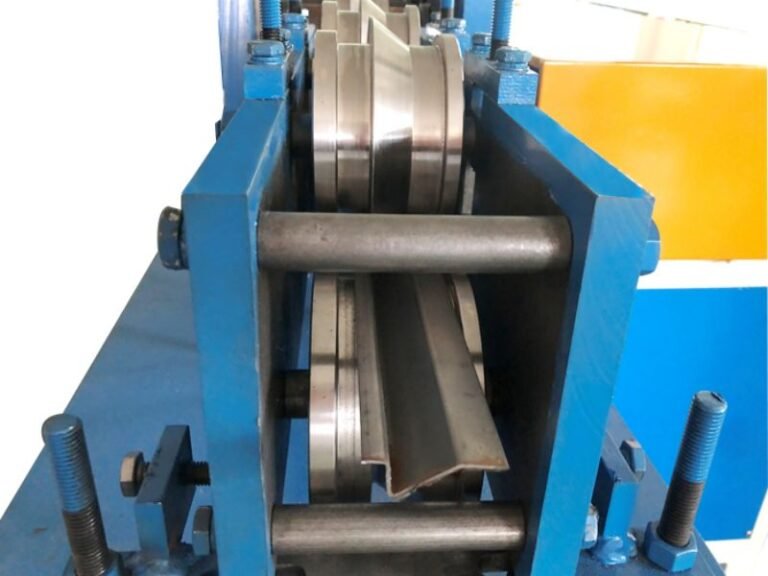
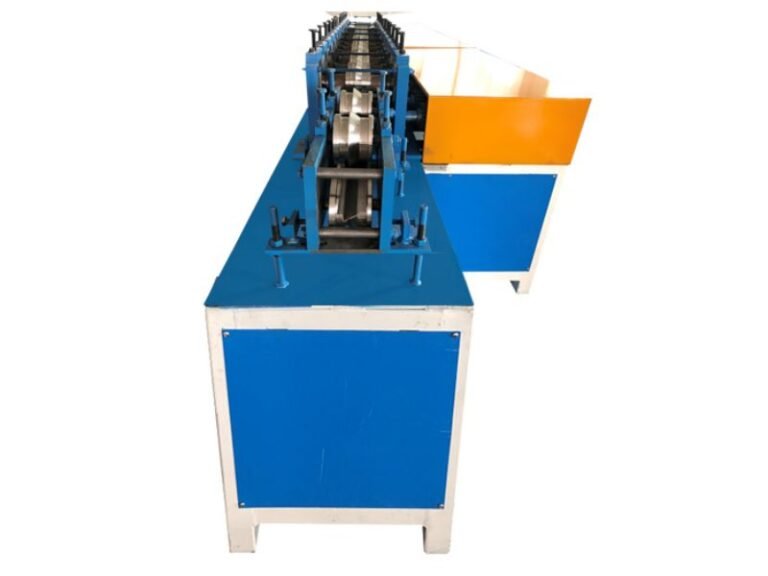
Advantages of our shelf back layer Roll Forming Machine
1. Good quality: we have a professional designer and experienced engineer team, we use good raw materials and accessories.
2. Good service: we provide technical support for the whole life of the machine.
3. Guarantee period: within one year from the end of commissioning. The warranty covers all electrical, mechanical and hydraulic components except vulnerable parts.
4. Simple operation: the whole machine is controlled by PLC computer control system.
5. Elegant appearance: rust proof, customized color
6. Reasonable price: we offer the best price in the industry.
Applications of shelf back layer Roll Forming Machine
Storage rack, storage shelf, Steel rack,steel shelf, rack beam, Shelf side panel
shelf back layer Roll Forming Machine Woring Process
Decoiler —– Leveling (Straightening) —– Roll Forming —– Punching —– Cutting —– Unloading
Or
Decoiler —– Leveling (Straightening) —– Punching —– Roll Forming —– Cutting —– Unloading
Components for shelf back layer Roll Forming Machine
Name | Quantity | Units | |
Decoiler | 1 | Set | |
Main Machine | Feeding device | 1 | Set |
Roll forming system | 1 | Set | |
Cut Equipment | 1 | Set | |
Hydraulic system | 1 | Set | |
Electric control system | 1 | Set | |
Supporter/Automatic Stacker | 1 | Set |
Main Technical Parameters of shelf back layer Roll Forming Machine
Main Technical Parameters: | |
Auto Machinery Equipment With PLC Control System | |
1. Manual Un-coiler | |
Max Capacity | 5000 kgs |
Inner diameter of coil | 400-600 mm |
Manual with brake | |
2. Leveling Device | |
Ensure the material level and straight | |
The width can be adjusted | |
3. Punching Device | |
Punching way | pre/post punching (pause to punch or Tracking) |
Material of punching mould | Cr12 with heat treatment |
Punching Mould | as per drawings |
4. Main Forming System | |
Max Feeding Width | as per drawings |
Product Max Effective Width | as per drawings |
Thickness of Panel | 0.2-2.0 mm |
Material Type | GI sheet coil or cold rolled coil or Aluminium etc. |
Diameter of Main Shaft | 95mm |
Rollers Station | 12 Rows |
Roller Material | C45 steel,Heat Treatment |
Surface of Roller | Chrome plating, Heat Treatment |
Driving Mode | By Chain and Gear Box |
Main Motor Power | 5.5 Kw |
Machine Body | Electrostatic Spraying Treatment |
Forming Speed | Min. 0-15 m/min |
The machine base is assembled and welded by high quality steel | |
5. Hydraulic Cutting System | |
Cutting Way | Pause to Cutting or Tracking (Flying) ,Non-stop |
Oil pump station | 1 set |
Hydraulic Oil Pump | CB-E310 |
Hydraulic Station Power | 7.5 Kw With Cooling System |
Blade Material | CR12 with heat treatment HRC60-62 |
Cutting mould | as per drawings |
Forced air cooling device available | |
6. Electrical System (PLC&HMI Control System) | |
Electrical System | PLC and HMI touch Screen (Taiwan Delta) |
Automatic Measuring Length Function Available | Yes, Rotary Encoder |
Automatic Counting Function Available | Yes |
Current Protection Function Available | Yes, Aviation Plugs |
Power Supply | 380V, 50Hz, 3 Phase (as per local requirement) |
7. Run-Out Table | |
Frame | 8# steel groove welded |
| roller type |
Quantity | 1 pc |
(They can be modified according to customer requirements) |
GET ONE-ON-ONE SERVICE
Free of charge to provide you with technical advisory services. Provide product samples, business profiles, credit certificates and other information. I invite customers to visit the company’s product design, product manufacturing process, product prototype, product testing facilities and quality management system