Home » Storage Rack Roll Forming Machine Collection » Shelf Stud Roll Forming Machine
Shelf Stud Roll Forming Machine
- Diameter Of Shaft: 80mm
- Thickness: 1.5~5mm
- Width: Max. 1000mm
- Punch: Online Punching
- Usage: Supermarket Warehouse Storage Rack Shelves
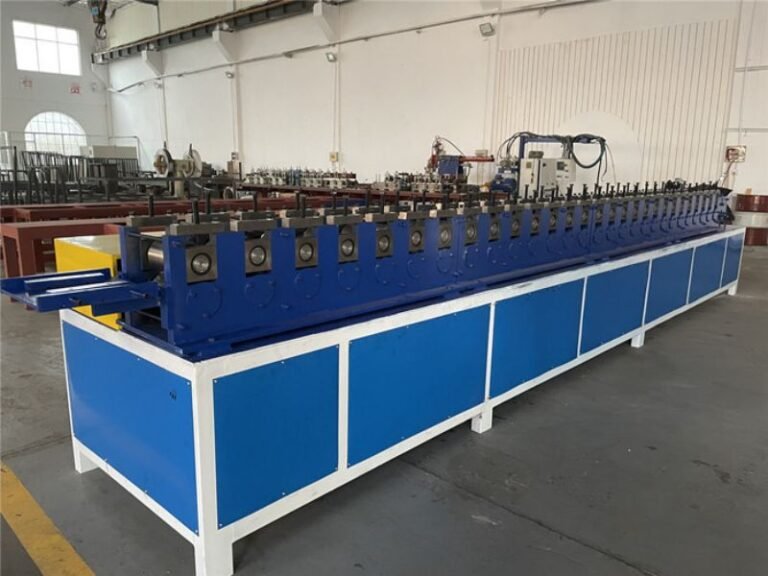
Features of Shelf Stud Roll Forming Machine
Function and structure: metal steel plate will through 20 rolls, the plate is gradually rolled into the finished bracket. It is composed of variable frequency motor, reducer and roller group. The bed adopts the welding structure to eliminate the stress.
The roller adopts combined structure, with small speed difference, small forming resistance and small steel plate surface wear.
The roller process design adopts imported software, computer design and finite element analysis to ensure the shape accuracy of the workpiece without scratching the steel plate.
The roll is forged with Cr12 and processed by numerical control after overall quenching. The hardness can reach HRC58-62. It has the characteristics of high strength, high hardness, high precision and long service life.
Main Technical Parameters of Shelf Stud Roll Forming Machine
1. Profile | .Thickness:2.0mm |
2. Process flow | Decoiling—feeding—leveling—punching—forming—cutting—production |
3. Manual decoiler | 1).Material coil inner diameter: 450mm-550mm |
4. Punching machine | 60t Automatic punch holes(with one set of mold) |
5. Forming system | 1).Number of forming steps:2 steps feeding rollers,4 steps leveling rollers, 12steps forming rollers, |
6.Cutting system | 1).Material: blade and mold material: Cr12 steel with quenched treated 60-62℃ |
7.Control system | 1). Screen: Delta screen from Taiwan |
8. Hydraulic | 1). Advanced hydraulic system from Taiwan |
9. Spare Parts | 1).Easy damaged parts: conk 2 pcs, fuse-link 4 pcs |
Description of Shelf Stud Roll Forming Machine
1. Manual coiler
Power: manual uncoiler, maximum capacity 5T
Applicable to coil inner diameter: 508mm
Applicable to coil maximum outer diameter: 1000mm
The manual power supply expands the inner surface of the coil.
2. Flying saw cutting
1) Continuous cutting;
2) The blade material is Cr12, which has been quenched.
3) Welded frame, good rigidity.
4) The cutting frame is heat treated to avoid deformation of the final product. Cut length tolerance ± 2 mm.
5) The cutting power is provided by the hydraulic station.
6) The final product can be cut according to the set length in PLC controller, and the length is automatically measured by encoder. When the final product reaches the set length, the machine will stop automatically cutting the product. When this is done, the machine will continue to run.
3. PLC control system
1) The system adopts delta programmable controller (PLC) to control all work actions. The production quantity and the length of each piece will be measured automatically. Easy to control roll forming machine.
2) Delta frequency converter speed control technology to achieve automatic production.
3) Enter the text screen and cancel the working data.
4) Friendly human-machine interface system, which can set the batch, length and quantity of workpieces.
5) Encoder counting, with the function of counting and measuring length.
6) Suitable power supply voltage: 380V / 50 Hz / 3 phase (can be designed according to the buyer’s requirements)
Related components
Name | Quantity | Units | |
Decoiler | 1 | Set | |
Main Machine | Feeding device | 1 | Set |
| Roll forming system | 1 | Set |
| Cut Equipment | 1 | Set |
| Hydraulic system | 1 | Set |
Electric control system | 1 | Set | |
Supporter/Automatic Stacker | 1 | Set |
Main Technical Parameters of Shelf Roll Forming Machine
1. Profile | .Thickness:2.0mm |
2. Process flow | Decoiling—feeding—leveling—punching—forming—cutting—production |
3. Manual decoiler | 1).Material coil inner diameter: 450mm-550mm |
4. Punching machine | 60t Automatic punch holes(with one set of mold) |
5. Forming system | 1).Number of forming steps:2 steps feeding rollers,4 steps leveling rollers, 12steps forming rollers, |
6.Cutting system | 1).Material: blade and mold material: Cr12 steel with quenched treated 60-62℃ |
7.Control system | 1). Screen: Delta screen from Taiwan |
8. Hydraulic | 1). Advanced hydraulic system from Taiwan |
9. Spare Parts | 1).Easy damaged parts: conk 2 pcs, fuse-link 4 pcs |
1. Profile | .Thickness:2.0mm |
2. Process flow | Decoiling—feeding—leveling—punching—forming—cutting—production |
3. Manual decoiler | 1).Material coil inner diameter: 450mm-550mm |
4. Punching machine | 60t Automatic punch holes(with one set of mold) |
5. Forming system | 1).Number of forming steps:2 steps feeding rollers,4 steps leveling rollers, 12steps forming rollers, |
6.Cutting system | 1).Material: blade and mold material: Cr12 steel with quenched treated 60-62℃ |
7.Control system | 1). Screen: Delta screen from Taiwan |
8. Hydraulic | 1). Advanced hydraulic system from Taiwan |
9. Spare Parts | 1).Easy damaged parts: conk 2 pcs, fuse-link 4 pcs |
Advantages
- Special shaped plate rolling machine
- Type B metal plate roll forming machine is made of thick metal plate by quenching and hardening roll quenching. Its shape includes W-type, C-type, freight car plate, high-speed rail, several word steel, closed steel, lace door frame, seamless steel pipe, ceramic heart-shaped column, etc. The production equipment of this product adopts flexible design and installation, with good sealing performance and low cost. The key of frame technology is the connection of three parts, the connection of frame and plate, the connection of beam and column, the connection of column and main body. A good product key is to deal with these three parts.
GET ONE-ON-ONE SERVICE
Free of charge to provide you with technical advisory services. Provide product samples, business profiles, credit certificates and other information. I invite customers to visit the company’s product design, product manufacturing process, product prototype, product testing facilities and quality management system