What Materials Are Used For Roll Forming?
The roll forming process refers to the process of forming various complex parts based on the plastic movement characteristics of materials and the principle of rolling extrusion.
Rolling deformation is a line contact, which is carried out continuously and step by step. The required deformation force is small. One stroke can produce one or several workpieces. Compared with the cutting and grinding processes, the roll forming process has not only high production efficiency and material saving, but also high product strength and stable quality. This process is especially suitable for processing workpieces with short advantages that are difficult to cut, especially for products with an annual output of millions of pieces in large quantities. The roll forming process is the most favorable and has the most considerable economic benefits.
Roll forming began in Europe in the 1960s. As the roll forming tool has the advantages of high production efficiency, saving materials, increasing product strength, etc., not only the application of threaded fasteners industry, but also the automobile, bicycle and other industrial departments use the roll forming process to process parts with complex shapes. With the development of technology and production, people pay more and more attention to the roll forming process.
Product characteristics
Compared with cutting and grinding processes, the roll forming process not only has high production efficiency and material saving, but also has high strength and stable quality. This process is especially suitable for processing workpieces with short specialties that are difficult to cut, especially for products with an annual output of millions of pieces in large quantities. The roll forming process is the most beneficial and has the most significant economic benefits.
Materials
The rolling process is a cold forging process. There are many materials that can be used for rolling forming, such as low-carbon steel, stainless steel, galvanized sheet, aluminum, etc. Among them, low-carbon steel is commonly used for rolling forming, and non-ferrous metals are more suitable for rolling forming.
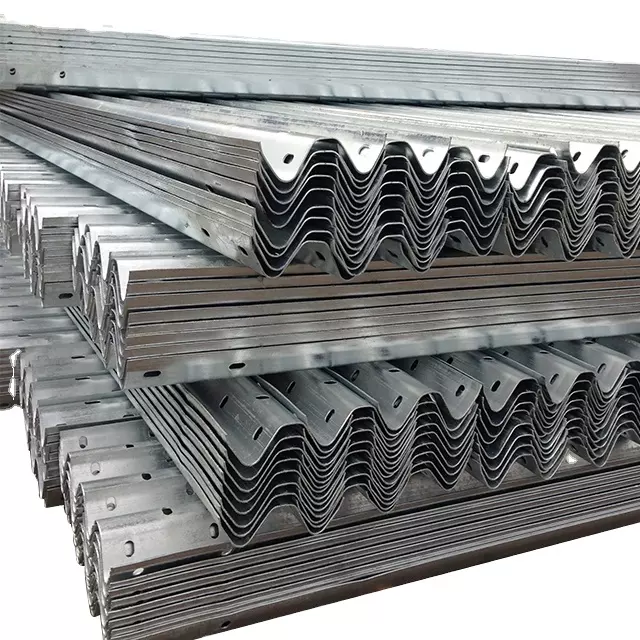
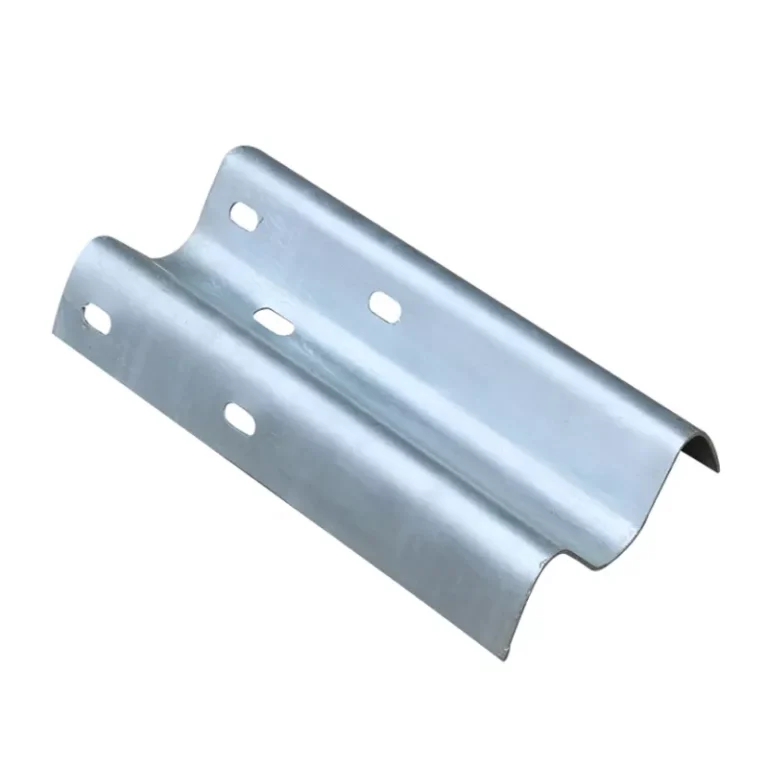
What aspects should be considered when selecting roll materials
The cold roll needs to bear large rolling cycle stress, strong friction, etc. in the working process. The working conditions of the cold roll mainly include:
(1) The roll surface shall have a high and uniform surface hardness, usually greater than 62HRC
(2) A deep hardening layer is required, and the hardness of the roll edge must be relatively low;
(3) The roll neck has low hardness
(4) The cold roll shall be able to resist cracking and spalling caused by torsional stress, bending stress and shear stress;
(5) It shall have high wear resistance, contact fatigue strength, fracture toughness and thermal impact strength.
The core part of cold roll forming equipment
Roll is the soul of cold roll forming. Our design features for roll are as follows:
(1) The average stress principle of each pass of the cold bending forming equipment, the average stress of the rollers of the whole line, balanced wear, and extended the service life of the rollers.
(2) The roll of the cold bending forming equipment is made of materials that use their properties, but the specific strength and hardness are contradictory. The red hardness of C12MoV should be used during heat treatment. After quenching, the hardness can be reached only after two or even three times of tempering.
(3) The circular arc of the track is the core part of the slide rail. The circular arc after the first few passes of pressing forming shall be protected by the tube bundle through the upper and lower rollers or cross wheels when the vertical edge is rolled and folded in the next pass. Otherwise, the circular arc position of the material will change during the stretching process, R will become smaller into a triangle, the steel ball will not reach the bottom, and the two point contact will generate noise. When R becomes larger, the mating rail will shake, and the track of the slide rail will be fuzzy when it is used, Uneven stress, slide rail deformation, shorten life.
(4) The problem of rolling stability is that materials often swing left and right in the raceway during production. In fact, a single group of rollers is asymmetrically loaded, and the force on the left side is large, so the materials swing to the right; The force on the right side is large, and the material swings to the left.